Among the various corrosions of stainless steel, the intergranular corrosion accounts for about 10%. It will reduce the bonding force between the grains. Under the action of stress, it is easy to crack and even break into powder, and it is very hidden. It is not visible on its appearance.
At the same time, it is also the main reason for inducing other corrosion. The intergranular corrosion of austenitic stainless steel is mainly caused by the lack of Cr in the grain boundary zone, and C easily forms compounds with Cr, which reduces the Cr content. For this reason, the preventive measures for intergranular corrosion are:
1. Chemical composition and organization
(1) C content
The C content in steel is the most important factor affecting the intergranular corrosion of austenitic stainless steel. On the one hand, strictly control the C content to control the carbon content of the base metal and welding rod below 0.08%; on the other hand, adding stabilizers such as Ti and Nb to the base metal and welding material has a strong affinity for C. The carbon is combined with Cr before it, and a stable compound is formed.
(2) Biphasic organization
dual-phase structure will greatly improve the ability to resist intergranular corrosion. On the one hand, adding ferrite forming elements, such as chromium, silicon, aluminum, molybdenum, etc., make the weld form a dual-phase structure; on the other hand, choose a welding material that contains more ferrite generators.
2, welding process
(1) The temperature is in the temperature range of 450~850℃, especially 650℃ is the most dangerous temperature zone (also known as sensitization temperature zone) where intergranular corrosion is most likely to occur. Therefore, when welding stainless steel, a copper plate under the weldment can be used, or water can be directly poured on the back of the weldment to cool it quickly, reducing the staying time in this temperature range, which is an effective measure to improve the corrosion resistance of the joint. .
(2) The increase of welding heat input will accelerate the corrosion of austenitic stainless steel. In the welding process, small current, high welding speed, short arc, multi-pass welding and other methods can be used to reduce the heat input. Adopt low welding heat input and quickly pass through the sensitized temperature zone to avoid intergranular corrosion in the heat-affected zone.
3, post-welding treatment
After welding, reheat the welded joint of austenitic stainless steel to 1050~1100℃, re-solution treatment, or reheat to 850~900℃, keep for 2h, and conduct homogenization treatment to eliminate the chromium-depleted area.
Please keep the source and address of this article for reprinting: Control of Intergranular Corrosion of Austenitic Stainless Steel
Minghe Die Casting Company are dedicated to manufacture and provide quality and high performance Casting Parts(metal die casting parts range mainly include Thin-Wall Die Casting,Hot Chamber Die Casting,Cold Chamber Die Casting),Round Service(Die Casting Service,Cnc Machining,Mold Making,Surface Treatment).Any custom Aluminum die casting, magnesium or Zamak/zinc die casting and other castings requirements are welcome to contact us.
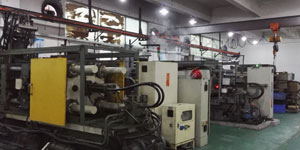
Under the control of ISO9001 and TS 16949,All processes are carried out through hundreds of advanced die casting machines, 5-axis machines, and other facilities, ranging from blasters to Ultra Sonic washing machines.Minghe not only has advanced equipment but also have professional team of experienced engineers,operators and inspectors to make the customer’s design come true.
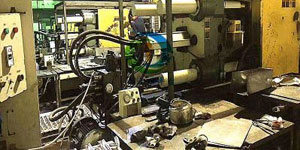
Contract manufacturer of die castings. Capabilities include cold chamber aluminum die casting parts from 0.15 lbs. to 6 lbs., quick change set up, and machining. Value-added services include polishing, vibrating, deburring, shot blasting, painting, plating, coating, assembly, and tooling. Materials worked with include alloys such as 360, 380, 383, and 413.
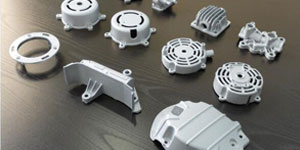
Zinc die casting design assistance/concurrent engineering services. Custom manufacturer of precision zinc die castings. Miniature castings, high pressure die castings, multi-slide mold castings, conventional mold castings, unit die and independent die castings and cavity sealed castings can be manufactured. Castings can be manufactured in lengths and widths up to 24 in. in +/-0.0005 in. tolerance.
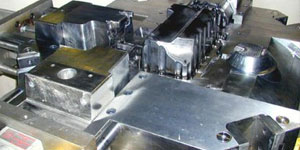
ISO 9001: 2015 certified manufacturer of die cast magnesium, Capabilities include high-pressure magnesium die casting up to 200 ton hot chamber & 3000 ton cold chamber, tooling design, polishing, molding, machining, powder & liquid painting, full QA with CMM capabilities, assembly, packaging & delivery.
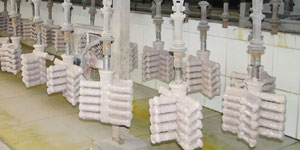
ITAF16949 certified. Additional Casting Service Include investment casting,sand casting,Gravity Casting, Lost Foam Casting,Centrifugal Casting,Vacuum Casting,Permanent Mold Casting,.Capabilities include EDI, engineering assistance, solid modeling and secondary processing.
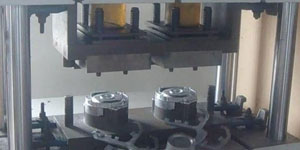
Casting Industries Parts Case Studies for: Cars, Bikes, Aircraft, Musical instruments, Watercraft, Optical devices, Sensors, Models, Electronic devices, Enclosures, Clocks, Machinery, Engines, Furniture, Jewelry, Jigs, Telecom, Lighting, Medical devices, Photographic devices, Robots, Sculptures, Sound equipment, Sporting equipment, Tooling, Toys and more.
What Can we help you do next?
∇ Go To Homepage For Die Casting China
→Casting Parts-Find out what we have done.
→Ralated Tips About Die Casting Services
By Minghe Die Casting Manufacturer |Categories: Helpful Articles |Material Tags: Aluminum Casting, Zinc Casting, Magnesium Casting, Titanium Casting, Stainless Steel Casting, Brass Casting,Bronze Casting,Casting Video,Company History,Aluminum Die Casting |Comments Off